Professional Guidance on What is Porosity in Welding and Just How to Address It
Professional Guidance on What is Porosity in Welding and Just How to Address It
Blog Article
Deciphering the Secret of Porosity in Welding: Tips for Lessening Problems and Maximizing Quality
In the detailed world of welding, porosity continues to be a persistent obstacle that can significantly influence the quality and honesty of bonded joints. As we dig right into the depths of porosity in welding, uncovering the tricks to its prevention and control will certainly be vital for specialists seeking to grasp the art of high-quality weldments.
Understanding Porosity in Welding
Porosity in welding, a common issue run into by welders, describes the visibility of gas pockets or spaces in the welded product, which can endanger the stability and quality of the weld. These gas pockets are typically caught during the welding process because of different variables such as improper securing gas, contaminated base materials, or inaccurate welding specifications. The formation of porosity can damage the weld, making it vulnerable to breaking and deterioration, inevitably resulting in architectural failures.
Comprehending the source of porosity is important for welders to successfully stop its incident. By identifying the value of maintaining proper gas securing, making certain the sanitation of base products, and optimizing welding settings, welders can substantially reduce the chance of porosity development. Furthermore, using techniques like preheating the base product, employing appropriate welding techniques, and carrying out comprehensive examinations post-welding can additionally assist in lessening porosity issues. In general, a comprehensive understanding of porosity in welding is necessary for welders to generate premium and durable welds.
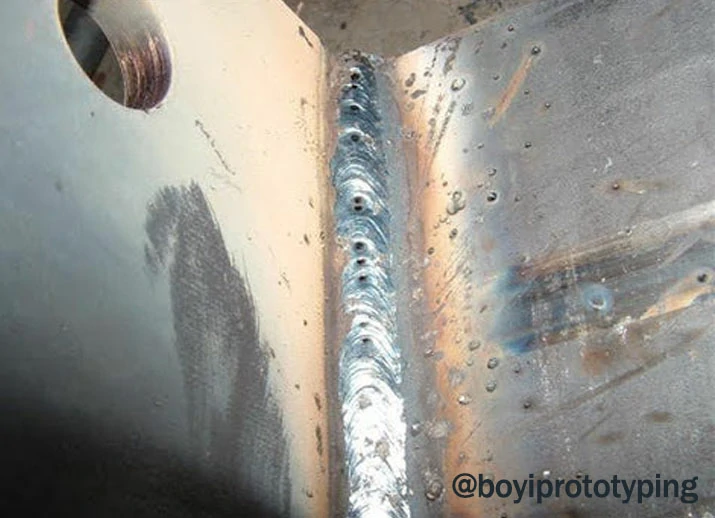
Typical Root Causes Of Porosity
When inspecting welding procedures for potential top quality issues, understanding the typical causes of porosity is necessary for keeping weld honesty and protecting against architectural failings. Porosity, characterized by the existence of cavities or gaps in the weld metal, can significantly endanger the mechanical residential properties of a welded joint.
Furthermore, welding at incorrect specifications, such as exceedingly high traveling speeds or currents, can generate excessive turbulence in the weld pool, trapping gases and triggering porosity. By resolving these typical reasons with proper gas shielding, material prep work, and adherence to ideal welding specifications, welders can reduce porosity and boost the top quality of their welds.
Strategies for Porosity Avoidance
Executing reliable precautionary steps is vital in minimizing the event of porosity in welding procedures. One method for porosity prevention is making sure correct cleansing of the base metal before welding. Impurities such as oil, grease, corrosion, and paint can cause porosity, so complete cleaning using proper solvents or mechanical approaches is necessary.

An additional key preventative procedure is the selection of the appropriate welding consumables. Utilizing top quality filler products and shielding gases that are suitable for the base metal and welding process can considerably decrease the risk of porosity. Furthermore, keeping proper welding criteria, such as voltage, existing, travel rate, and gas circulation price, is vital for porosity avoidance. Differing the advised setups can lead to improper gas protection and inadequate fusion, leading to porosity.
Additionally, utilizing correct welding strategies, such as maintaining a constant travel rate, electrode angle, and arc size, can assist avoid porosity (What is Porosity). Sufficient training of welders to ensure they adhere to ideal methods and high quality control treatments is also vital in decreasing porosity problems in welding

Ideal Practices for Quality Welds
One trick method is keeping correct sanitation in the welding location. Completely cleaning up the workpiece and bordering location before welding can help reduce these problems.
One more ideal method is to carefully choose the appropriate welding parameters for the particular materials use this link being joined. Appropriate criterion selection ensures optimum weld penetration, blend, and general quality. Making use of top notch welding consumables, such as electrodes and filler steels, can dramatically influence the last weld top quality.
Relevance of Porosity Control
Porosity control plays an important duty in making certain the stability and top quality of welding joints. Porosity, identified by the visibility of tooth cavities or voids within the weld steel, can considerably compromise the mechanical buildings and architectural honesty of the weld. Excessive porosity damages the weld, making it a lot more look here prone to splitting, corrosion, and total failure under functional lots.
Effective porosity control is necessary for maintaining the desired mechanical residential properties, such as strength, ductility, and durability, of the bonded joint. What is Porosity. By decreasing porosity, welders can boost the overall high quality and integrity of the weld, making certain that it satisfies the efficiency requirements of the desired application
In addition, porosity control is essential for accomplishing the preferred aesthetic look of the weld. Excessive porosity not just weakens the weld yet also diminishes its aesthetic allure, which can be get redirected here crucial in industries where appearances are very important. Proper porosity control methods, such as using the correct shielding gas, regulating the welding specifications, and making sure correct tidiness of the base products, are important for generating top notch welds with very little defects.
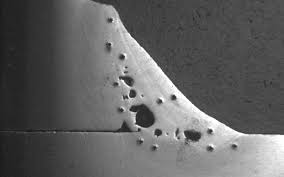
Verdict
In final thought, porosity in welding is a common flaw that can compromise the quality of the weld. It is necessary to manage porosity in welding to make sure the integrity and toughness of the final product.
Report this page